無(wú)錫不銹鋼板廠家無(wú)錫漢能不銹鋼2020年6月7日訊 不銹鋼制件具有良好的抗高溫氧化性、抗腐蝕性,在五金、餐飲、醫(yī)療及航空航天等領(lǐng)域應(yīng)用廣泛,需求也不斷增加,對(duì)該類(lèi)制件的表面質(zhì)量要求越來(lái)越高。相比于其他鋼材,不銹鋼具有屈服強(qiáng)度高、屈強(qiáng)比小、均勻延伸率大、硬化指數(shù)高的特點(diǎn),正是由于這些特點(diǎn),不銹鋼板料拉深成形性能良好,但是容易出現(xiàn)制件起皺、開(kāi)裂和模具零件粘結(jié)瘤等缺陷。通過(guò)調(diào)整模具結(jié)構(gòu)和成形工藝參數(shù),制件起皺與開(kāi)裂能有效避免,但模具零件粘結(jié)瘤的形成機(jī)理比較復(fù)雜,目前沒(méi)有較好的解決方案,這是不銹鋼制件在拉深成形過(guò)程中的難題。從宏觀角度觀察,板料表面與模具零件表面無(wú)縫貼合,載荷作用于接觸面上。從微觀角度觀察,板料表面與模具零件表面均凹凸不平,二者實(shí)際工作狀態(tài)為非連續(xù)接觸,載荷實(shí)際作用于局部凸起部位,如圖1所示。
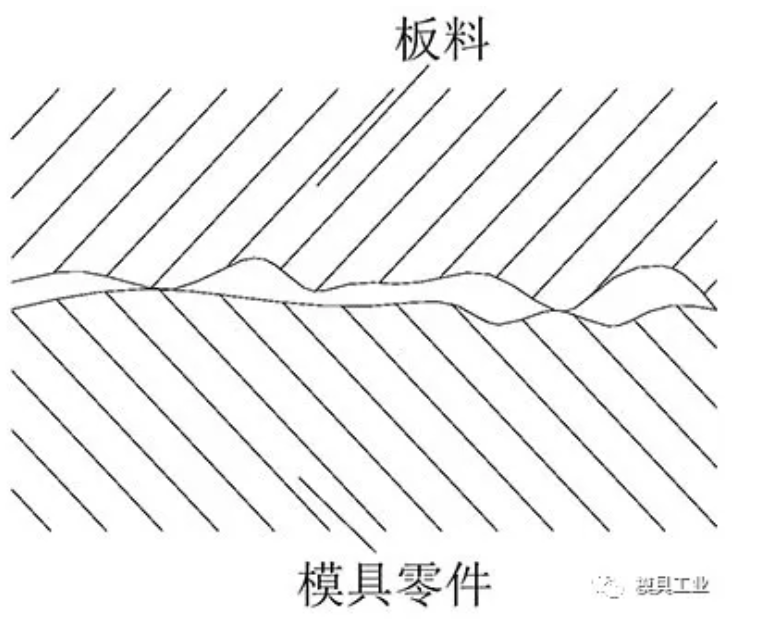
圖1 板料與模具零件接觸面微觀狀態(tài)
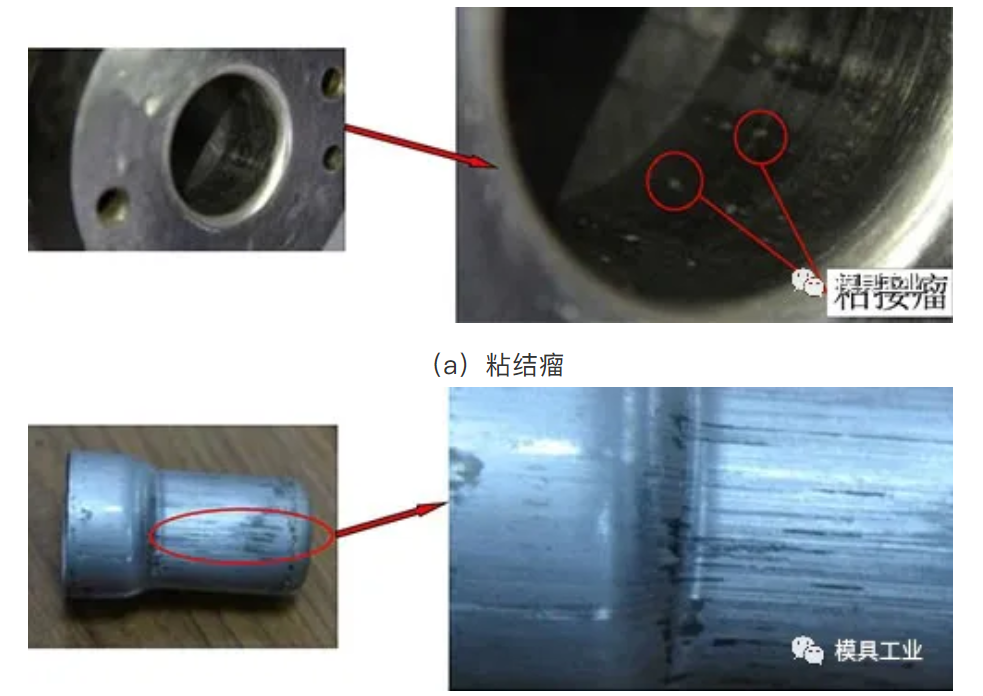
(b)制件表面劃傷
圖2 模具零件的粘結(jié)瘤與制件表面劃傷
由于不銹鋼材料的特性,成形時(shí)需要較大的壓邊力,實(shí)際工作狀態(tài)下,潤(rùn)滑油承受高溫、高壓及運(yùn)動(dòng)剪切力,局部潤(rùn)滑油膜易變薄、破裂,出現(xiàn)干摩擦區(qū)域,摩擦力瞬間增大。板料表面局部凸起與模具零件表面凸起均受到與運(yùn)動(dòng)方向相反的剪切力,最終板料凸起部位被刮掉。在高溫、高壓的環(huán)境下,板料材質(zhì)與模具零件材料親和力較好,碎片將軟化、熔化、枯焊在模具零件表面上,碎片隨拉深的進(jìn)行不斷粘附在模具零件表面上,最終形成粘結(jié)瘤,成形的制件表面被劃傷,如圖2所示。由粘結(jié)瘤的形成過(guò)程可知,其產(chǎn)生與高溫、高壓、摩擦、材料親和力有較大的關(guān)系。由于高壓與制件材料性質(zhì)有關(guān),不可更改,防粘結(jié)瘤方案的選擇只能從高溫、摩擦、材料親和力3個(gè)方面考慮。
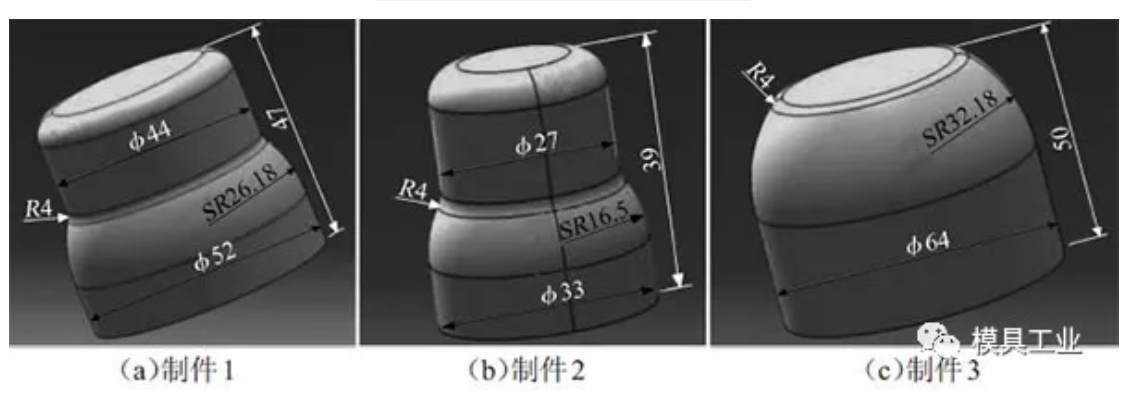
圖3 不銹鋼制件
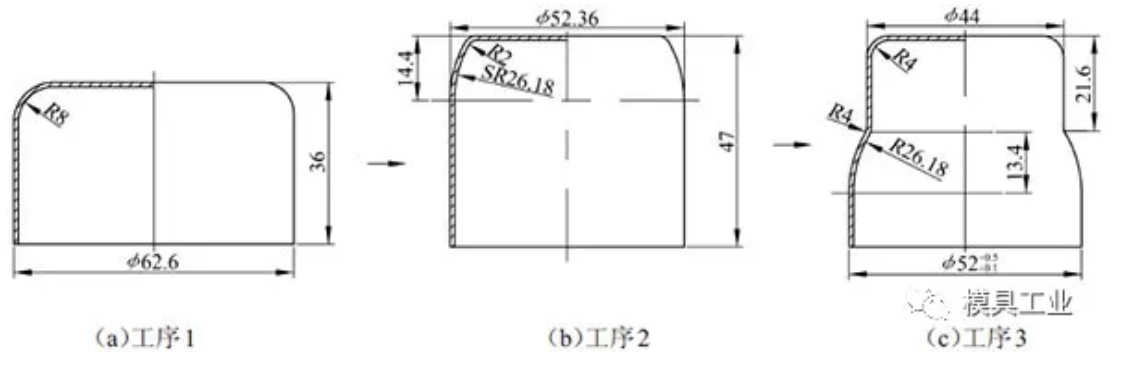
圖4 制件1拉深工序
試驗(yàn)所成形的不銹鋼制件如圖3所示,均由圓筒形、球形組成的復(fù)合形式階梯型制件,材料均為1Cr18Ni9Ti,料厚均為1mm,其中,制件1的坯料直徑為?107mm,3次拉深成形工序件的尺寸,如圖4所示。拉深模工作部分零件材料選擇T8A或Cr12MoV等,粘結(jié)瘤問(wèn)題較嚴(yán)重。模具零件表面與成形制件表面均出現(xiàn)嚴(yán)重劃傷,模具返修率較高。針對(duì)粘結(jié)瘤形成機(jī)理,不銹鋼拉深模防粘結(jié)瘤方案擬采用以下2種方式。
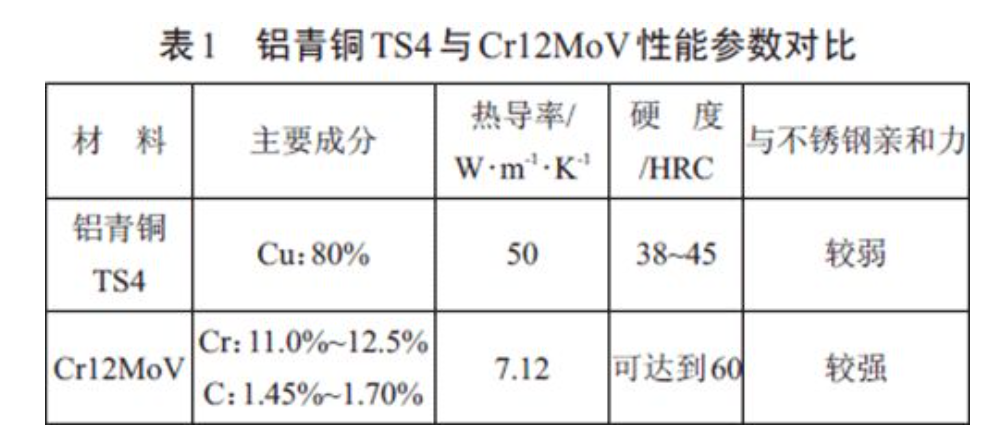
研究發(fā)現(xiàn),銅合金作為模具零件材料具有導(dǎo)熱性能好、耐磨性好、無(wú)需表面處理、與不銹鋼親和力較弱等優(yōu)點(diǎn)。鋁青銅TS4作為銅基合金中的一種,具備上述優(yōu)點(diǎn)。鋁青銅TS4的性能參數(shù)與Cr12MoV對(duì)比如表1所示,鋁青銅TS4作為不銹鋼拉深模零件材料,成形過(guò)程中能快速散熱、避免粘結(jié),有效避免粘結(jié)瘤的產(chǎn)生。
| TD表面超硬化處理技術(shù)的應(yīng)用TD處理即熱擴(kuò)散法碳化物覆層處理(thermal diffusion carbide coating process),是通過(guò)高溫?cái)U(kuò)散作用于模具零件表面形成一層數(shù)微米至數(shù)十微米的金屬碳化物覆層的表面處理技術(shù)。該覆層具有較高的硬度,熱處理硬度可達(dá)3600HV左右。由于TD處理溫度高達(dá)1000℃,材料受限,多適用于含碳量高于0.3%的各類(lèi)鋼材。研究發(fā)現(xiàn),對(duì)Cr12MoV冷作模具鋼進(jìn)行TD處理,表面VC涂層與不同摩擦副配對(duì),發(fā)現(xiàn)與鋼柱配對(duì)時(shí)摩擦因數(shù)最小,磨損率最低。經(jīng)過(guò)TD處理的零件工作部分耐磨性增高、摩擦系數(shù)降低、抗咬合性能增強(qiáng),同時(shí)該部分表面粗糙度等級(jí)高,提高了材料的抗粘合性。TD處理與傳統(tǒng)工藝的主要參數(shù)及性能對(duì)比如表2所示。
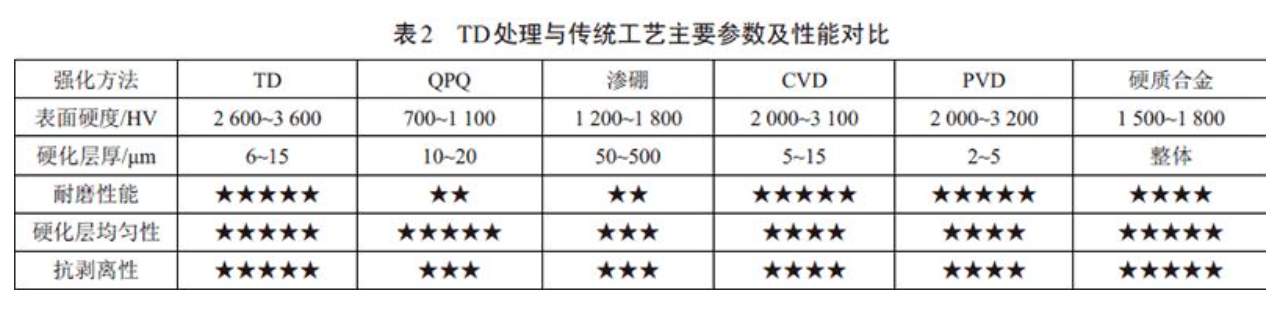
目前防止產(chǎn)生粘結(jié)瘤的研究大多數(shù)集中于鋁青銅TS4等模具零件材料與潤(rùn)滑油的研究,而將TD處理運(yùn)用于不銹鋼制件多次拉深模上,特別是將TD處理與鋁青銅TS4組合運(yùn)用,該類(lèi)研究還未見(jiàn)報(bào)道。模具結(jié)構(gòu)設(shè)計(jì)
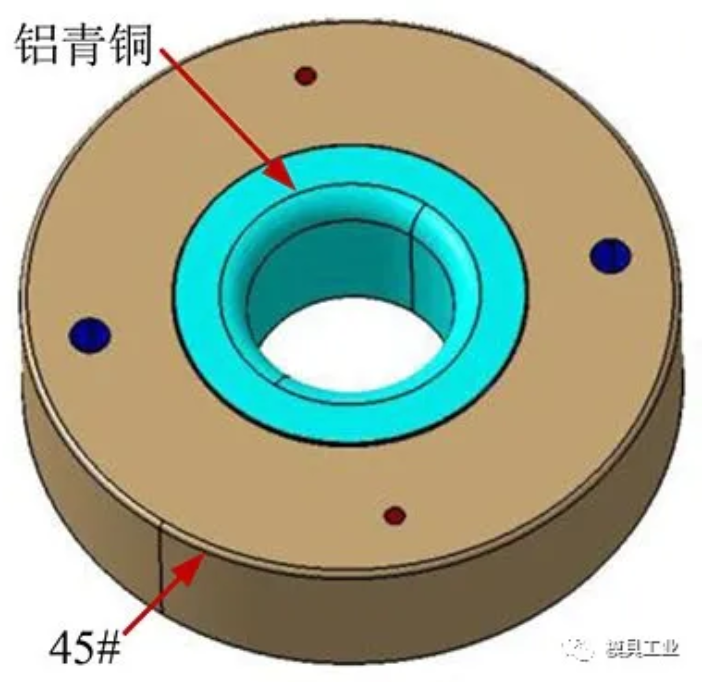
(a)凹模(壓合式)
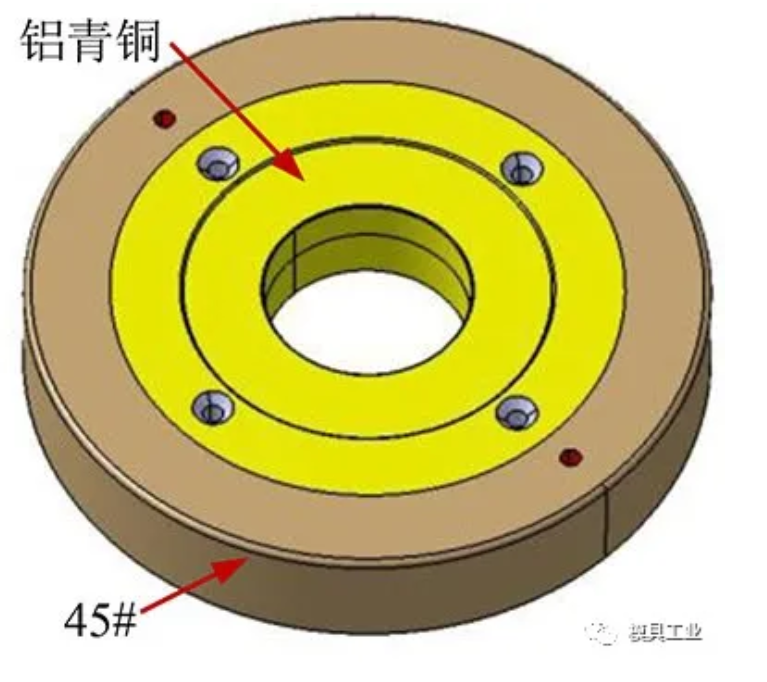
(b)壓邊圈(螺釘連接式)
圖5 鑲拼結(jié)構(gòu)
(1)鑲拼結(jié)構(gòu)。由于鋁青銅脆性大、可加工性能差、價(jià)格高。試驗(yàn)中需使用鋁青銅TS4材料的模具零件部分均采用鑲拼結(jié)構(gòu),內(nèi)置鑲件采用鋁青銅,外緣采用45#鋼。根據(jù)使用鋁青銅的模具零件部位不同,鑲拼結(jié)構(gòu)又分為壓合式(鑲件帶有錐度)與螺釘連接(鑲件無(wú)錐度)2種方式。試驗(yàn)中凹模均采用壓合式,壓邊圈采用螺釘連接方式,鑲拼結(jié)構(gòu)如圖5所示。
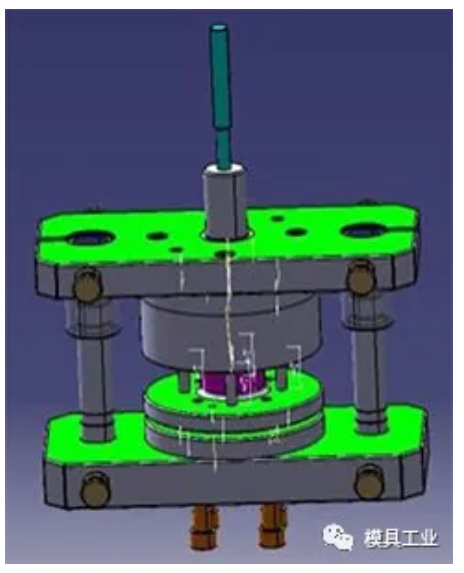
(a)拉深模三維模型
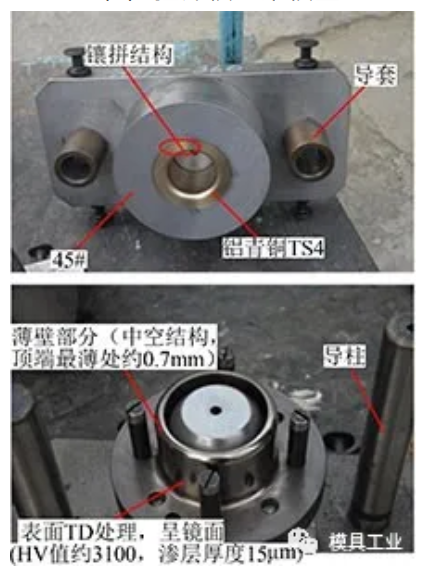
(b)實(shí)際模具
圖6 拉深模三維模型及實(shí)際模具
(2)導(dǎo)柱導(dǎo)套。無(wú)導(dǎo)向裝置的拉深模在機(jī)床上安裝合模時(shí),需要反復(fù)調(diào)試。初始拉深成形的若干件制件均會(huì)報(bào)廢,浪費(fèi)時(shí)間和浪費(fèi)材料,為了解決上述問(wèn)題,試驗(yàn)中拉深模上下模導(dǎo)向裝置采用導(dǎo)柱導(dǎo)套(左右兩導(dǎo)柱直徑不同),如圖6所示。拉深模主要工作部分包括凹模、凸模、壓邊圈等。由于凹模及壓邊圈與不銹鋼板料之間存在相對(duì)滑動(dòng)且承受較大的載荷,粘結(jié)瘤現(xiàn)象嚴(yán)重。凹模與壓邊圈需要進(jìn)行防粘結(jié)瘤設(shè)計(jì):工作部分選擇鋁青銅TS4材料(無(wú)熱處理)或含碳量大于0.3%的普通鋼材并進(jìn)行TD超硬化表面處理;凸模與不銹鋼板料之間無(wú)相對(duì)滑動(dòng),無(wú)粘結(jié)瘤的產(chǎn)生,凸模選擇一般材料及熱處理方式即可(試驗(yàn)選擇Cr12MoV材料,熱處理硬度56~60HRC)。
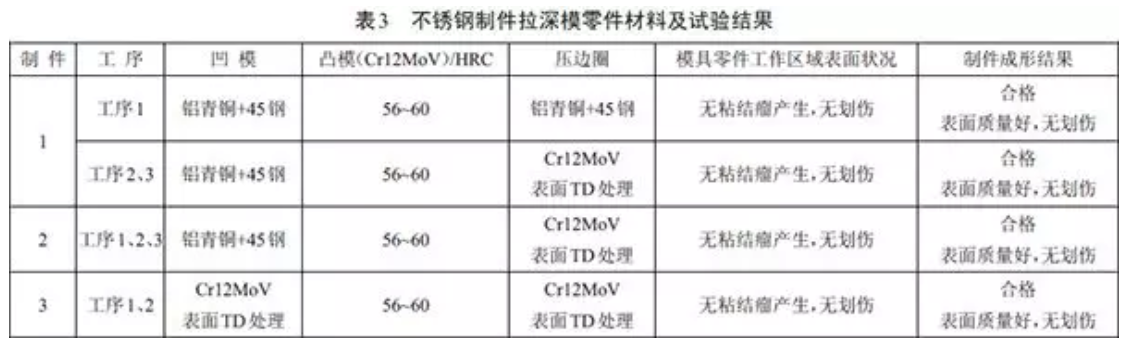
試驗(yàn)所選用研究對(duì)象均需多次拉深的階梯型不銹鋼制件,除工序1外的其他所有工序,壓邊圈處均存在薄壁部分(中空結(jié)構(gòu)),最薄壁厚處僅約0.7mm(見(jiàn)圖6)。由于鋁青銅硬度38~45HRC,脆性大,拉深過(guò)程中容易發(fā)生脆裂,具有薄壁特征的壓邊圈不宜采用鋁青銅TS4,應(yīng)選用TD處理技術(shù),成形所用的8副拉深模零件材料及其表面處理方式如表3所示。一般為了減少或防止粘結(jié)瘤的產(chǎn)生,不銹鋼拉深模需使用特殊研制的潤(rùn)滑劑,如2#潤(rùn)滑油、納米銅潤(rùn)滑劑、丙烯酸清漆等。由于模具零件工作部分使用鋁青銅TS4與TD超硬化表面處理技術(shù),潤(rùn)滑劑選擇普通種類(lèi)即可,試驗(yàn)所用潤(rùn)滑劑為聚氯乙烯。運(yùn)用三維建模軟件CATIA,完成拉深模的三維數(shù)字模型設(shè)計(jì)。經(jīng)檢測(cè),試驗(yàn)中經(jīng)過(guò)TD處理的模具零件表面呈現(xiàn)鏡面,硬度約3100HV左右,滲層厚度達(dá)15μm,拉深模三維模型及實(shí)物見(jiàn)圖6。
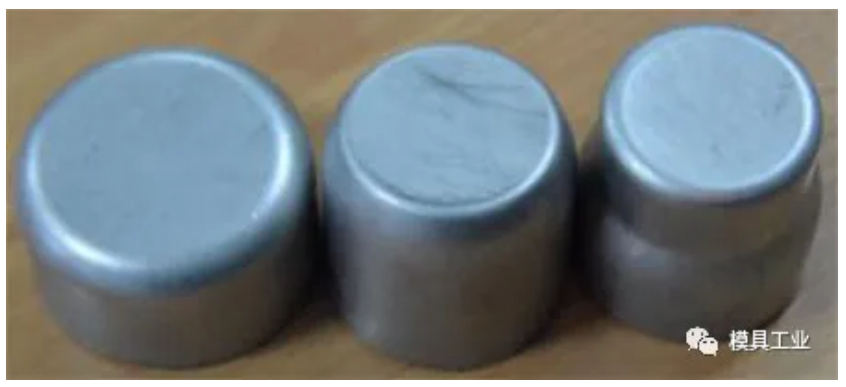
(a)制件1
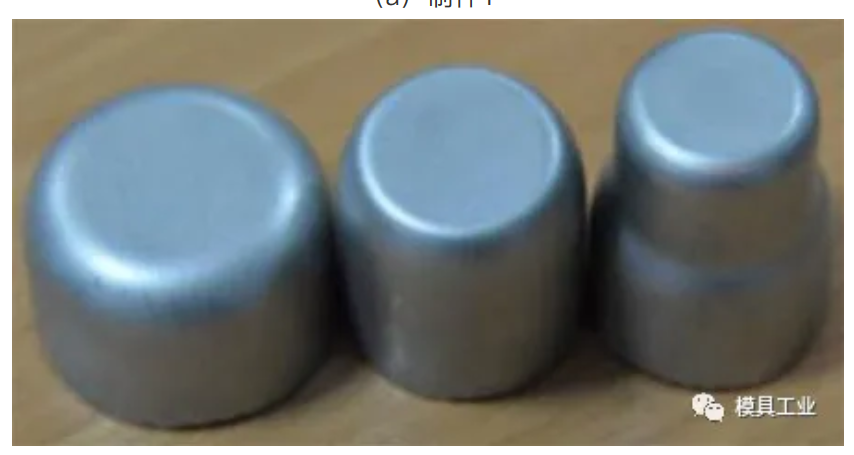
(b)制件2
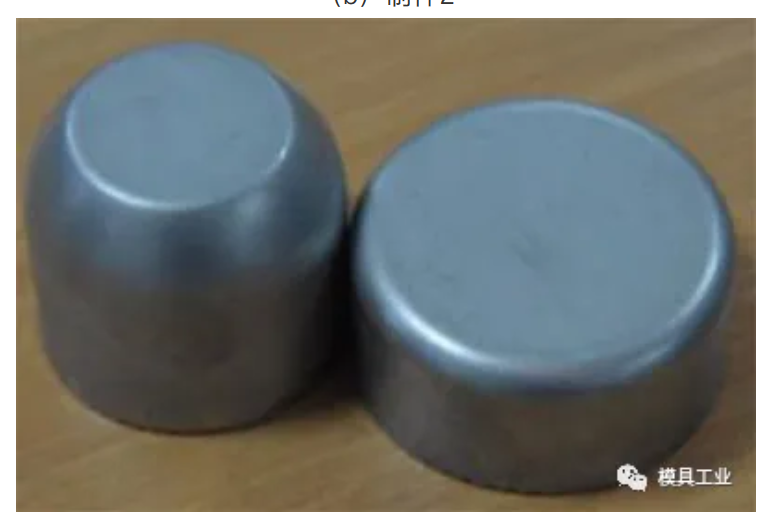
(c)制件3
圖7 拉深成形不銹鋼制件
在1000kN機(jī)床上進(jìn)行拉深模試模,每副拉深模試制成形7件不銹鋼制件,完成8副拉深模(總計(jì)56個(gè)制件)試模僅用1天(8h),拉深成形不銹鋼制件實(shí)物如圖7所示。
▍原文作者:李欣芮1,2,王曉康1,2,何萬(wàn)飛1,2
▍作者單位:1.成都飛機(jī)工業(yè)(集團(tuán))有限責(zé)任公司技術(shù)裝備公司;2.四川省航空智能制造裝備工程技術(shù)研究中心